The best ereaders for 2025
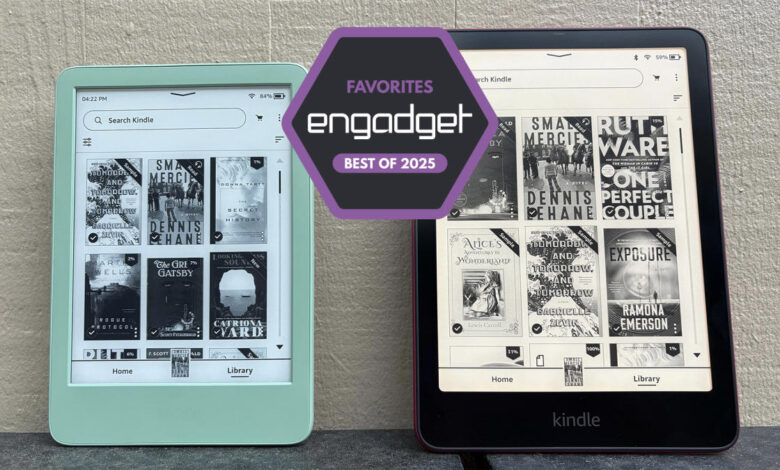
If you just want a way to read ebooks, you already have what you need in your pocket with your smartphone. But if you want something that’s less distracting and easier on your eyes, you may want to go with an ereader instead. As it stands, the market is currently dominated by two brands. Amazon’s Kindle has captured the largest share by far, but Rakuten Kobo devices are a winning alternative — in fact, the Kobo Clara Colour is our current top pick. Smaller companies like Onyx Boox and PocketBook produce Android tablets with e-paper screens that can do more than just display books.
Other considerations, such as whether or not you need a color display or the ability to write on the screen for note-taking, will determine which ereader to buy. Factors like library size, compatibility with rights-managed content and more also come into play. Over the past two years, we’ve tested out more than a dozen devices to create a guide to help you pick the best ereader for you — and help you get the most out of your new gadget once you get it.
Table of contents
The best ebook readers for 2025
Screen size: 6” | Display type: Black/white and color E Ink | Resolution: 300 dpi black & white, 150 dpi color | Capacity: 16GB| Battery life: Weeks | Waterproof rating: IPX8 (submergible to 6 feet for 60 minutes) | Warm light: Yes | Lock screen ads: No
Read our full Kobo Clara Colour review
Our previous pick for this category, the Kobo Clara 2E was an excellent ereader with a crisp display, a warm glow and responsive, intuitive touch controls all housed in a waterproof design that felt premium. When Rakuten announced the Clara would be updated, I worried we’d see Kobo device with superfluous revamping to justify an inflated price. Thankfully, that’s not the case. The Kobo Clara Colour not only adds color and a faster processor, it’s just $10 more than the previous generation.
As the name suggests, this ereader adds color to the page, lending a little vibrance to book covers, tables and graphs, and even the panels of graphic novels. The technology comes from E Ink, in the form of the Kaleido 3 module that incorporates a color filter layer on top of the standard black and white microcapsule layer. That results in two different resolutions on one screen: 150 dpi for color and 300 dpi for text.
Full-color pages remind me of comic book art from the ‘60s, muted but saturated. Color makes book covers more enticing and adds a little variety to headings, and tables in some non-fiction books. It’s certainly not a necessary feature, but it adds vibrance and it’s fun.
There is a slight difference in clarity between the color and non-color version of the Clara. If you look closely, you can see a bit of noise on the white parts of the page. That’s due to the added color filter layer. It’s not distracting and only something I noticed when comparing the two generations side-by-side. but if absolute clarity is your primary goal, you may be better off with a non-color ereader.
Probably the more useful upgrade here is the dual 2GHz processor, a bump from the Clara 2E’s 1GHz CPU. There’s a noticeable improvement in the speed of the page turns and navigating from the menu to the page and back again is nearly instantaneous. As with the 2E, the Colour rarely mistakes a swipe for a tap or a page turn gesture for a menu request.
The adjustable warm front light is still here (it’s actually a little warmer on the Colour) and makes reading at night easy on the eyes. The operating system is the same, with intuitive access to the Kobo store, your personal books and titles from your local library via Overdrive. You can customize your reading experience with options for font, font size, line spacing, margins and so on. Kobos don’t have a way to save a group of display settings like the Kindle does, so I’d love to see that added with future OS upgrades. But for now, the customizations are just enough to get your book how you want it to look.
The Colour is nearly identical in shape and size, and has the same premium feel as the 2E, though the plastic has a grainier finish. The bezels are noticeably less flush with the screen now, though that didn’t alter my reading enjoyment.
Now that it costs $150, the Kobo Clara Colour is $40 more than the base model Kindle. But the waterproof build, warm front light, responsive controls and lack of ads (which cost $20 to get rid of on Amazon’s device) make it worth it. And, in great news for the right to repair crowd, it’s even designed to be user-repaired once it falls outside of warranty through a partnership with iFixit.
Rakuten still makes the Kobo Clara BW, which is nearly identical to our previous “best overall” pick. It doesn’t suffer from the slight clarity loss that the color overlay presents, but it also still has the older processor.
Of course, if you already own a mountain of Kindle books, you may want to stick with Amazon’s system. In that case, the best Kindle is Amazon’s Kindle Paperwhite. It costs $160 and was recently updated with a more powerful processor and new E Ink tech that makes it exceptionally speedy while displaying high-contrast text. The warm light is great and the flush front screen feels premium. One more consideration, now that Amazon now has its own color model too, is the Colorsoft, but at $280, it’s significantly more expensive than the Clara Colour and even the Paperwhite Signature Edition.
- Customizable settings
- Even more responsive touch controls
- Color is pleasant and text is crisp
- Kobo’s store not as vast as Kindle’s.
Screen size: 6” | Display type: Black/white E Ink | Resolution: 300dpi | Capacity: 16GB | Battery life: 6 weeks | Waterproof rating: None | Warm light: No | Lock screen ads: Yes
If you just want to read books, and have no need for the perks that the fancier ereaders bring (color, waterproof rating, warm light, etc), then the base model Kindle is for you. The six-inch, non-flush display is housed in a textured plastic that feels less premium than, say, the Paperwhite or even the two Kobos on our list, but still feels plenty durable. And it’s small enough to fit in a coat or back pocket making it very travel-friendly.
It’s unfortunate that the 2024 model is $10 more than the 2022 model when not much has changed, but it’s still the cheapest ereader from any of the major manufacturers. And if we know one thing about Amazon, it’s that the company loves a good sale, so you’ll likely find it on discount if you can hold out for Prime Day or Black Friday deals.
The reader is a no-frills gateway to the best of what the Kindle ecosystem has to offer, including Kindle Exclusive titles, with books by established authors as well as newer, self-published writers; Kindle Unlimited offers the widest selection of any subscription-based reading service out there; and Audible Originals is made up of narrated titles and podcasts you can only hear through a Kindle device or Amazon-owned app.
If you like to switch between audiobooks and ebooks, Kindle is the way to go. When you buy both iterations of a title, you not only get a discount, but the Whispersync feature lines up where you are in the e-printed version with the narration, too. Say you listen for an hour and then want to read – the synchronization lets you pick up on-screen where you left off audibly. (Though we should point out that you can’t listen and read simultaneously on the same device.) In tests, the feature was fairly accurate, getting me close enough on the page or in the audio to figure out my spot.
Page turns are quicker on the new model but I’m disappointed that there’s still no way to adjust the zones and responses to touchscreen gestures, like there is on both Kobo and Boox devices. Kindles all have a very narrow strip on the left for going back a page and I’m constantly missing it and going forward instead. Though swipes generally work well.
Probably the most noticeable missing feature is the lack of warm light. Compared to any ereader with that option, the screen on the standard Kindle appears harsh and bluish, but it’s still far easier on your eyes than a phone or tablet screen. There’s plenty of customization for the font, size and margins, too. You can even save your settings as a “theme,” something not offered by other devices. I created one with larger text and wider line spacing called “tired eyes.”
Some people won’t be bothered by the lock screen ads that come standard on this Kindle (unless you pay $20 to remove them). They’re fairly innocuous, mostly promoting Kindle book deals or specific titles (it’s not like you’ll see promos for TVs or robotic pool cleaners). Personally, I like being able to set the sleep screen to the book cover of what I’m currently reading, but it’s easy to get over that if all you want is a more convenient way to consume books at the lowest price.
- The most affordable ereader
- Compact and durable build is highly portable
- Grants access to Kindle’s vast ebook catalog plus library books
- Best integration between audio and text
- No warm light
- Not waterproof
- Can’t read third party ebooks
Screen size: 7” | Display type: Black/white and color E Ink | Resolution: 300 dpi black & white, 150 dpi color | Capacity: 32GB | Battery life: Weeks | Waterproof rating: IPX8 (submergible to 6 feet for 60 minutes) | Warm light: Yes | Lock screen ads: No
When Kobo came out with the new Clara Colour, it also debuted the new Libra Colour, which might be the more exciting of the two devices. In addition to color technology from the E Ink Kaleido panel and an upgraded processor, the Libra now has stylus support. It’s the only ereader on this list with that feature, making it a lot like a small E Ink tablet — but all of its new features actually make it a better ereader.
When I wrote about the previous generation ereader, the Libra 2, I was impressed by how comfortable it was for reading. None of that has changed; the buttons and auto-rotating screen adapt the device to just about any reading position you chose and the thin design, textured back and soft-touch plastic give it a premium feel.
Kobo’s interface is nearly the same here as with other models, nicely organized to let you easily find your current reads or browse and search new titles from Kobo’s store or your local library in the Overdrive tab. The customizations for light and text let you get the page looking just how you like it, but there aren’t so many options that it feels like you’re writing code.
The new features add to the experience. In color, book covers all look more enticing — though, if your TBR list is already three feet long, this won’t not help things. The new processor makes waking from sleep, turning pages, navigating the menu and changing orientation zippy fast.
Then there’s the status compatibility. Try as they might, some new technologies don’t yet beat their real-world counterparts. That’s mostly how I feel about styluses — I’m just a big fan of pen on paper. But Kobo’s stylus makes it so fun to highlight text and scribble notes in the margins of a book that I’m starting to come around. Plus, it neatly and magnetically attaches to the side so it doesn’t get lost.
Pressing and holding the button on the side of the stylus highlights text while flipping it around erases. I accidentally pressed the button a few times when I was trying to write, but I got used to the placement after a few minutes of using it. You can pick from four different highlighter colors and view your written notes and spotlighted text in the notes section of any title — which I could see being pretty useful for book club reads, school assignments or just refreshing yourself on a past read before you dive into the sequel.
Writing in the margins or directly on the text worked on every book I tried. Though I should point out that if you change the font size in a book, your handwritten notes will be converted to a sticky note-type box. Going back to the original font restores your original scribbles.
The Kobo Libra Colour is $30 more expensive than the Libra 2, but you get a lot for $220. If it were just an ereader, the lovely colors, responsive reading experience, fast page turns and easy highlights would make it worth the price. But you also get features that make it more than just an ereader, like Dropbox and Google Drive integration, a beta web browser and free-writing and text-converting notebooks.
Of course, the stylus costs extra and you won’t get features like notebooks and writing in the margins without it. Together, the set costs $290, which is a considerable $110 cheaper than the recently updated (and most popular) stylus-enabled ereader the Amazon Kindle Scribe. That one has a bigger, 10.2-inch screen, which is nice for writing but, for me, is a little big for an ereader. The Libra Colour on the other hand has just the right features at the right size, plus some extras that stretch its usefulness.
- Premium build that’s comfortable to hold
- Crisp text and lovely colors
- Responsive and intuitive touch controls and buttons
- Adding the stylus allows for margin notes
- Kobo’s store is less vast than Kindle’s
Screen size: 6” | Display type: Black/white E Ink | Resolution: 300dpi | Capacity: 32GB | Battery life: 12 weeks | Waterproof rating: IPX8 | Warm light: Yes, auto adjustable | Lock screen ads: No
Read our full Kindle Paperwhite Signature Edition review
When I reviewed the new Kindle Paperwhite Signature Edition, I was struck by the elevated reading experience it provided. It’s remarkably fast, the text is wonderfully crisp and it has a premium design that feels great to hold. Amazon was able to improve page turn and scrolling speeds for both the standard Paperwhite and the Signature Edition by giving them new processors and using an oxide thin-film transistor layer to enable faster changes on the page. The layer also allows for better display clarity than other transistor layers.
Both the standard and Signature models have warm front lights that cast a lovely glow across a screen that’s a little larger now at 7-inches (up from 6.8 last time). The battery life is longer, promising up to 12 weeks (instead of 10), meaning you’ll rarely need to charge your ereader. Despite that, the Paperwhite models are actually three millimeters thinner than the previous generation (and just a touch heavier).
With the Signature Edition, you also get auto-adjusting front lights that dim or brighten as daylight fades or you move from room to room. The storage capacity goes up from 16GB to 32GB, so even if you download a whole bunch of audiobooks, you aren’t likely to run out of space too quickly. And finally, you get a wireless charging option for the periodic occasions when it’s time for a refill. All of those features are nice to have, though not necessary — but for anyone who wants to read ebooks in the most luxe way possible, the Signature model is the one to go for.
If you want an experience that’s nearly as deluxe, but don’t need the wireless charging, auto-adjusting lights and extra capacity specs, the non-Signature Paperwhite is still noticeably more premium than the standard Kindle, with a larger screen, ultra-crisp text and a luxurious build. Plus you still get access to all the perks that only Kindles offer, like Goodreads integration, Kindle Exclusive titles, Kindle Unlimited subscription books and Whispersync tech that lines up your audio and ebook reads so you can swap between the two formats.
There’s also the Amazon Kindle Paperwhite Kids, which is the same gadget, but comes with a cover, a longer warranty and a six-month subscription to Amazon Kids+.
- Screen displays crisp text with a lovely warm light
- Flush-front screen and soft-touch back feel premium
- Noticeably faster page turns and scrolling
- Auto-adjusting warm front light is helpful
- Power button on the bottom edge is easy to accidentally trigger
- Can’t adjust touch screen controls
- Fewer page and font adjustments than the competition
- The features exclusive to the Signature aren’t essential
Screen size: 7” | Display type: Black/white and color E Ink | Resolution: 300 dpi black & white, 150 dpi color | Capacity: 64GB | Battery life: Weeks | Waterproof rating: splash-resistant | Warm light: Yes | Lock screen ads: No
Color E Ink screens are the “new” thing in ereaders — even though the tech has been commercially available since around 2010. E Ink announced its Kaleido 3 display in 2022, and with the right combination of color saturation and clarity, it’s now appealing enough for general consumption. The latest ereaders from Boox, Kobo have color screens, and, finally in 2024, Amazon launched its own color model, the Colorsoft.
The Boox Go Color 7 (from Amazon, Boox) is a natural choice to supplant our previous winner in this category. The Boox Page is still available, and represents a great multipurpose tablet that easily handles ereader and tablet duties. The new Go Color not only layers color on top of that, it also has double the storage capacity, an extra gig of RAM and ships with Android 12. The back is also textured instead of slick, an upgrade my accident-prone fingers are grateful for. And all of this comes at the same $250 list price as the Page.
Boox stuck a faster quad-core processor in the Page. That made for a noticeable uptick in speed when compared to the reader’s predecessor, the Leaf 2. This looks to be the same CPU in the Go Color and I haven’t noticed a huge speed difference with the new reader — though it’s plenty fast. The battery has the same 2,300mAh capacity, but ereader batteries last the order of a few weeks, so an upgrade in that department wasn’t really necessary.
The Go Color 7 runs on a fork of Android 12, which allows it to act more like a tablet than a conventional ereader. Like all Boox devices, this approach is best suited for the tech-savvy. Unlike a Kindle or Kobo, which come preconfigured with a store to buy books from a digital library as well as easy borrowing from your local library system, Boox ereaders offer little hand-holding in setup and usage. While there is a store, it’s made up of public domain titles — most people will read books by uploading ePubs manually or through ereader apps like Kobo, Kindle, Libby and others from the built-in Google Play store.
Boox’s built-in ereader app, NeoReader, is nicely featured with a good amount of control over the look of the text. But it only handles DRM-free ePubs from sites like Project Gutenberg or publishers like Tor. If you want to read ePubs with digital rights management, which make up the vast majority of current ebooks, you’ll need to use a different app. Ironically, I’ve been using PocketBook’s ereader app to read DRM ePubs I bought from third parties.
The tablet is impressively customizable, with programmable buttons and fine-tunable settings. Boox users have created APK files to tweak and improve the experience further. The device even has a microphone and speakers, and can run apps like Spotify. In short, the Go Color 7 can do far more than a typical ereader can, if you’re willing to experiment.
The reading experience is enhanced with a soft, adjustable front light with temperature control that makes for pleasant low-light reading and the flush, glare-free, screen is lush and detailed. Like all color ereaders, you do give up a modicum of clarity to accommodate the color array, and the warmth is noticeably more yellow. I only noticed the contrast when I set comparable ereaders side-by-side and, really, it’s the difference between a super duper crisp screen and only a super crisp screen.
The soft and muted colors have a saturated look like watercolors or old comic book illustrations. Comparing the same book cover on the Kobo Clara Colour and this, the Boox hues do look a touch grainier and less rich. But that’s a small sacrifice if you need an ereader that can do far more than just carry your books around.
- Capable, customizable tablet
- Supports multiple ereader apps
- Solid build with a muted color screen
- Not easy for beginners
- Native ereader app doesn’t support DRM files
- Built-in store is only public domain titles
Screen size: 6.13” Resolution: 300 dpi | Capacity: 128GB | Water resistant: Yes, splashes and spills | Warm light: Yes | Lock screen ads: No
Boox makes two sizes of its ereader. The Poke 5 is smaller than the Page, doesn’t have buttons and goes for about $80 less. But after trying it, I don’t recommend it. It’s laggy and getting the Google Play Store to work was a pain. Once I did, page turns in apps like Kindle were excruciatingly slow.
The Boox Palma, however, is quite fun. It’s the same size and shape as a smartphone and, in a lot of ways, acts like one. The home screen is a muted black and white version of what you might find on a standard Android — you can even add a few widgets. Like the Page, it can download and run apps from the Google Play Store and has speakers to play music and videos. The E Ink screen (a Carta 1200) renders text crisply, but images, particularly moving ones, look far grainier and rougher than they would on a real phone’s LCD or OLED screen. That said, the video quality is the best I’ve seen on an E Ink screen, thanks to a software improvement Boox calls Super Refresh Technology.
But make no mistake, it’s not going to replace your phone. Wi-Fi and Bluetooth are the only connectivity and the 16MP camera is just for making document scans you can convert to PDFs. But the phone-like build is comfortingly familiar and the E Ink screen is lovely to read. At $280, it’s more expensive than a standard ereader — and some E Ink tablets — but it’s a highly portable way to read Kindle, Kobo, Google Books and other ePubs, while also handling simple games and apps like a smartphone. If you’re sick of the glow of your handset, the Boox Palma is a charming alternative.
What to look for in an ereader
Plenty of apps, including the Kindle app, will let you download and read digital books on a phone or tablet. But what makes ebook readers different is the screen: nearly all of them use technology from a company called E Ink. It manufactures electronic paper displays (EPD) composed of three sheets: one containing millions of microcapsules filled with black and white ink particles sandwiched between transparent electrode layers. When a charge is applied, either the black or white particles shift to the top, forming letters and the whitespace around them.
Color ereaders add a color filter array on top of the standard black and white microcapsule layer. The result is two different resolutions on one screen — the color clarity is 150 dpi while black and white images and text are still 300 dpi.
Because these displays are so different from standard backlight LED panels, you can expect most ereaders to do a number of things well. They’ll be easier to stare at for long periods of time and easier to read in direct sunlight. Also, since E Ink displays only require power to rearrange the ink, these devices have much longer battery lives than even the best tablets: we’re talking weeks on a single charge, not days.
The ereader market is not as saturated as, say, the smartphone market, but there are still plenty of options out there and they do have small but important differences among them. They tend to range from around $100 to more than $400, though usually the higher end options are stylus-enabled read/write E Ink tablets like the Kindle Scribe. Beyond price, you should consider physical properties like buttons, lights, storage and resolution, as well as how the software lets you find and access books.
Reading features
With any ereader, you’ll navigate the OS via taps and swipes, and some add physical page-turn buttons. Most with built-in buttons have an auto-rotating screen so you can press with your right or left hand.
As E Ink technology has advanced, resolution has greatly improved – even the budget Kindle ereader has a 300 ppi display. You can still find models with lower resolution, but we don’t recommend them.
Some ereaders have front LEDs that support light temperature adjustment. That means you can switch to a warmer light after the sun goes down, which will feel easier on the eyes. If you’re concerned about blue light, you should go for a reader with that feature. Finally, dark mode is available on most later model ereaders, allowing you to invert the black and white text and background, which some people find easier to read in low-light settings.
Other features
The capabilities of these pocket libraries have advanced considerably since the early days. In addition to storing books, some let you browse the web, run apps and play music. The screen’s frame rate can’t handle gaming, but it’s good enough to show you the Wikipedia entry for Striver’s Row while you read Crook Manifesto.
If you listen to audiobooks, you may want a Bluetooth-enabled ereader capable of playing them. Most of the models we tested have that ability, with the notable exception of the Nook ereader we tried. Keep in mind that audiobook files can take up more space than print files so you’ll probably want a device with a higher storage capacity if you plan on doing a lot of listening.
Above all, you should consider where and how you intend to find books to read. Most ereaders make it easiest to shop through their own digital bookstores, but all of them (even Kindles) will now let you download titles from other sources, like libraries, unaffiliated ebook sellers and free public domain sites.
How to get books for your ereader
Kindle, Nook and Kobo all have their own stores that you access directly from each brand’s devices. Prices are the same among all sellers, too. Publishers set the price of an ebook, not the retailer, so a title will cost the same at Amazon, Barnes & Noble, eBooks.com and the Kobo store.
Amazon offers Kindle Unlimited for $12 per month, and it includes four million titles from which you can pick your next read. It includes audio and ebooks, but you won’t find many big, new releases or older bestsellers. Kobo has a subscription called Kobo Plus with about 1.3 million titles: it goes for $8 per month for ebooks only, $8 for audiobooks only or $10 for both.
Buying a book from a proprietary store instantly delivers it to your device, provided you’re connected to WiFi. It also syncs your reading across devices and apps, so you can pick up where you left off on your phone if you forgot your ereader at home. It truly is the most convenient way to go, but if you don’t want to be locked into one brand’s store, or if you opt for an ereader without its own marketplace, you do have options.
How to upload ePubs onto an ereader
Stores like ebooks.com and Google Play have millions of ebooks for sale as digital rights-managed (DRM) ePub files, which Kobo, Nook and PocketBook readers can read in their native ereader apps. Kindles don’t support DRM ePub files at all and Boox devices require third party reading apps (of which there are many) to read those files. Titles from Apple Books are only readable in iOS devices.
Titles from some publishers like Tor and public domain classics from sites like Project Gutenberg are also sold as ePubs, but without the added DRM. Consequently, Kindles and the Boox Neoreader do support those files. Books you get from third-party sources will look just like ones you bought from a proprietary store, thanks to the flowable, formatted nature of ePub files. While these device-agnostic ebook collections give you extra options for finding your next read, they require a few additional steps to get the files onto your ereader.
To do so, you’ll typically need a computer running a free program called Adobe Digital Editions (ADE). After buying and downloading the ePub file, open ADE and plug your ereader into your computer (all readers here have a USB-C port for charging and data transfers). Your device should pop up in the left panel. Drag and drop the ePub file from your downloads folder into the main panel in ADE. The file will display as an image of the book cover. Drag that image onto your device on the left panel. If the file includes digital rights management (which protects against unauthorized copying) you’ll need to authorize your ereader, which requires using or creating a free Adobe ID. Once you’ve finished adding files to upload, eject the reader from your computer to complete the transfer process.
Kindles use a web-based uploader instead of the ADE method. But since Kindle uses its own proprietary DRM technology instead of Adobe’s, the only files it can accept from third parties are non-DRM files, such as from Tor Publishing or Project Gutenberg. After downloading a compatible ePub file, drag and drop it into your browser with the Send to Kindle page open. As long as you’re signed into Amazon, this wirelessly transfers the files to your associated device.
Boox also uses a browser uploader called BooxDrop (along with many other methods) to deliver ePubs to the device. Open it from the Boox App menu and you’ll see a device-specific url. Type that into your browser to access a file delivery portal that uploads to your library. Boox’s built-in ereader app, NeoReader, also doesn’t support files with DRM, so you won’t be able to read current titles from most publishers using that app. Fortunately, Boox devices run nearly every ereader app out there, Kobo and Kindle included, letting you access ePubs any number of ways.
Recently, Bookshop.org, the online seller of physical books that supports indie bookstores, started selling ebooks and up to 100 percent of the profits will go to local booksellers. The company uses a different rights management system than ADE so, right now, you can only read titles you buy from them on the Bookshop.org app, but the company is working with the makers of both Kindle and Kobo to extend compatibility to those ereaders.
How to read library books on an ereader
Your local library card lets you borrow audio and ebooks through a program called Overdrive and its companion app Libby. On a Kobo, you have have built-in access to Overdrive in a separate tab. Once you’ve linked your public library card, the search function will include results for titles available from your local library system; a few taps will upload your selections to your device for the length of the loan. I personally find it easiest to borrow the title I want through the Libby app on my phone. After that, the book pops up on my Kobo’s home screen once the device syncs.
To read library books on a Kindle, you can either go through the Libby app or the Overdrive section of your library’s website. Once you click Borrow, you’ll see the option to “Read now with Kindle,” which takes you to Amazon’s site to sign in. After that, the book will be delivered to your device the next time it connects to WiFi.
For other ereaders, you’ll go through your library’s Overdrive portal and download the ePub after clicking the Borrow button. You can then use the ADE process we described above. Devices that run external apps, like Boox’s Page, Go Color 7 or Palma, allow you to read library books via the Libby app, just as you would on a smartphone or iPad.
You can also use the Libby app to borrow audiobooks, but you won’t be able to access them through your ereader. (The exception is an ereader, like a Boox device, that allows external apps). I found it was easier to listen to an audiobook on my phone anyway, regardless of whether I borrowed it through Libby or bought it from Kindle or Kobo.
How we test ereaders
When putting together any guide, the first thing we do is spend hours researching the field. We look at what’s available, what’s new, and what shoppers and professional reviewers have to say. Then we narrow a list to the best candidates for hands-on testing.
Over the course of the past two years, I’ve tested just over a dozen ereaders, representing five different brands: Amazon, Kobo, Barnes & Noble, Boox and PocketBook. I bought, borrowed and uploaded books for each device using the methods above. I used each one for between a few days to a few months. I evaluated each one in the areas of book access, ease of reading, extra features and overall value. Here’s everything we tested so far:
Other ereaders we tested
Amazon Kindle Colorsoft
Amazon’s first color Kindle impressed with its quick page-turns and load times, auto-adjusting front light and, of course, a decently striking color E Ink display. But at $280, it’s more expensive than all of the other color ereaders in its size range, including the Kobo Libra Colour and the Boox Go Color 7.
Also, some Colorsoft owners reported seeing a yellow band at the bottom of their ereader’s display. This issue did not affect our first review unit during the original testing period, but it eventually appeared. An Amazon spokesperson told Engadget: “A small number of customers have reported a yellow band along the bottom of the display. We take the quality of our products seriously—customers who notice this can reach out to our customer service team for a replacement or refund, and we’re making the appropriate adjustments to ensure that new devices will not experience this issue moving forward.”
Amazon sent us a new Colorsoft ereader at the end of 2024 and it does appear that the fixes the company made resolved the yellow-band issue. The screen on our second review unit appears warmer overall, but not overly so. It’s more akin to the screen on the Kobo Libra Colour, and that’s a good thing.
Ereader FAQs
Which ereaders can read Kindle books?
Amazon’s Kindle ereaders are the obvious answer, but other devices capable of running apps can also read titles from the Kindle store. For example, you can download the Kindle app on a Boox ereader through Google Play (the store comes standard in the Boox app menu). You can then sign into your Kindle account and access all the books in your library — the same way you’d read Kindle books on your phone or tablet.
Can you buy Kindle books without a Kindle?
Yes. You can buy Kindle books through the Kindle app or through Amazon’s website via a browser. You can read those titles on a Kindle or any device that can run the Kindle app, such as a smartphone, tablet or computer. Just be aware that Kindle titles can only be read through one of Amazon’s ereaders or the Kindle app. The company uses proprietary digital rights management on all ebooks it sells that can’t be read by other ereader apps like Kobo or Adobe ADE.
What’s the difference between Kindle and Kobo?
Both Kindle and Kobo are brands of dedicated ereaders that support searching, buying, downloading and reading ebooks from their own stores. Both also support borrowing books from your local library via Overdrive and Libby.
The difference is that Kindle is owned by Amazon and uses the Kindle store, whereas Kobo is owned by Rakuten and its books come from the Kobo store. Both stores come pre-loaded as a tab on their respective ereader and both carry most in-print books. Each store also carries their own exclusive ebooks as well, but Amazon’s library of Kindle-only books is much larger than Kobo’s. Amazon also offers Amazon Original stories to read on the Kindle, which are free short fiction and nonfiction reads that are free to Prime members.
Which ereader is best for library books?
Both Kobos and Kindles have simple systems for borrowing library books. Other ereaders, like Boox, let you borrow books after downloading the Libby App. Only Kobo ereaders let you search for and borrow books directly on the ereader, with a dedicated Overdrive tab. Kindles, on the other hand, utilize a convenient “read on Kindle” function from the Libby app or website. You can send a borrowed book to your Kindle just by signing into your account. Both methods are pretty easy, so which is the best for you probably depends on other factors than just the library-book feature.
Recent updates
March 2025: Added news about Bookshop.org getting into the ebook market. Updated information about price-setting by publishers.
January 2025: Updated the “Others we tested” section to include impressions of the second Kindle Colorsoft review unit we received.
August 2024: Replaced our Android tablet pick with the new Go Color 7 ereader from Boox. Updated book titles to current examples. Added an FAQ section to explain the difference between Kobo and Kindle ereaders and further detail library-book support on different models.
November 2024: Following the release of Amazon’s new Kindle ereaders, we tested and reviewed the Kindle Paperwhite Signature Edition, the base-model Kindle and Amazon’s new color ereader, the Kindle Colorsoft. Accordingly, we updated our budget pick, added a premium pick and noted our experience with the Colorsoft.
https://s.yimg.com/ny/api/res/1.2/Fq1a1.J_mnEae68QXQF_Nw–/YXBwaWQ9aGlnaGxhbmRlcjt3PTEyMDA7aD02NzU-/https://s.yimg.com/os/creatr-uploaded-images/2024-12/5e3431d0-bd35-11ef-8fef-643ec576b8e0
2025-03-28 02:01:27