Improving designer and manufacturer collaboration using RIM
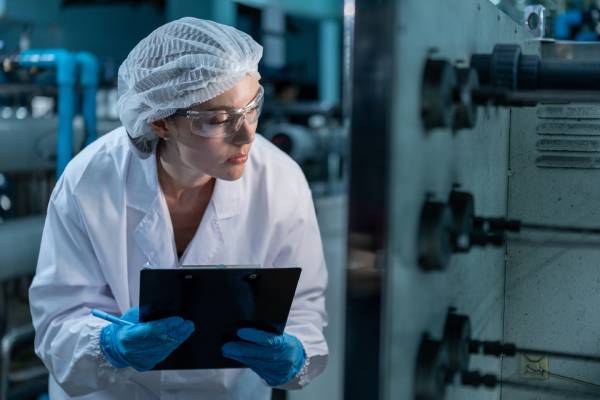
AD
Strong collaboration between designers and manufacturers is imperative for smooth product development, but challenges often arise when moving from concept to production. Reaction injection molding (RIM) provides a powerful way to improve workflows, boost efficiency, and bring designs to life with greater accuracy. Its benefits are especially evident in applications like medical devices and lab equipment, where advanced solutions are a priority.
Understanding reaction injection molding in collaboration
More than just a method for molding parts, RIM offers a dynamic, adaptable process that supports design teams throughout development. With the use of engineering quality materials and low-pressure molding, it enables cost-effective modifications and fine tuning. By working together, designers and manufacturers can accelerate prototyping, align on critical features, and simplify the shift to mass production.
Here are five benefits of using RIM to enhance teamwork:
1. Incorporates design flexibility early
Design revisions often come up after initial concepts meet prototype realities. RIM allows intricate detailing and multifunctional designs, while remaining cost-effective for low volume production. This flexibility means designers can adapt their ideas without compromising the capabilities of the manufacturing team, opening the door to smoother iterations.
2. Combines complex geometries and lightweight materials
For many projects, the challenge lies in finding materials that are durable and lightweight. RIM delivers on both fronts, producing complex parts with consistent wall thicknesses that optimize performance without adding unnecessary weight. This reliability fosters smooth collaboration, giving both designers and manufacturers confidence in the final product.
3. Accelerates prototyping and testing
Effective prototyping bridges the gap between teams’ expectations. Reaction injection molding accelerates tooling, delivering initial models faster. This rapid turnaround supports designers in testing features and refining designs collaboratively, eliminating unnecessary setbacks to keep progress steady.
4. Handles oversized or large components
RIM’s low-pressure process makes it particularly effective for creating durable, large-scale components. By evenly filling molds and minimizing defects, it eliminates production delays, fostering smoother communication between manufacturers and designers who can focus on the integrity of their designs.
5. Offers seamless integration with low volume production
Collaboration often falters when scaling from prototype to low-volume production. RIM’s ability to adapt to smaller production runs resolves these issues, keeping design and manufacturing teams synchronized and promoting a seamless transition without confusion or missteps.
By fostering proper communication and leveraging RIM’s advantages, teams avoid common challenges that might arise with other methods, especially when weighing what to consider when choosing a part molding process. This is because RIM inherently supports revisions, creative freedom, and reliable outputs while prioritizing speed and efficiency.
Aligning designer and manufacturer efforts doesn’t have to be complicated. Improving collaboration using RIM helps teams on the same page faster, enhances workflows, and helps bring innovative ideas to life with precision and flexibility.
Discover more from Heartland Newsfeed
Subscribe to get the latest posts sent to your email.
https://i0.wp.com/www.heartlandnewsfeed.com/wp-content/uploads/2025/01/Rimnetics-333424-Worker-Inspecting-Machinery-Image1.jpg
2025-01-14 12:16:48